Bauforschung und Innovation : Neue Technologien für ressourcenschonendes Bauen zur Marktreife entwickelt
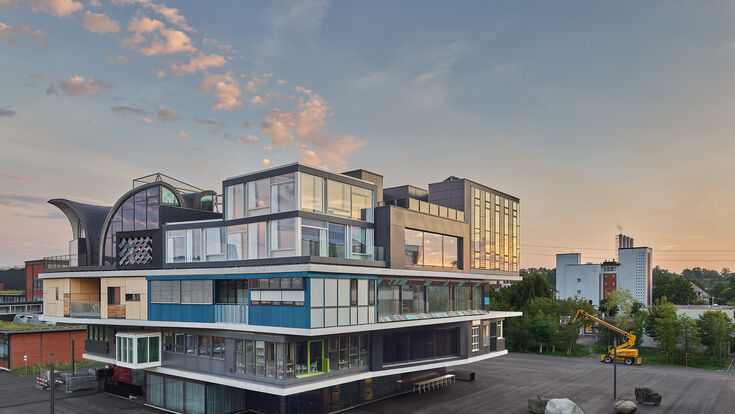
Die Unit "Step2" wurde am letzten Augusttag 2024 eröffnet.
- © Zooey Braun, Roemerstraße 51, 70180 Stuttgart Tel. 0049-(0)711-6400361 zooey@zooeybraun.deMit dem modularen Forschungs- und Innovationsgebäude NEST setzt sich die schweizerische Empa gemeinsam mit über 150 Partnern aus Forschung, Wirtschaft und der öffentlichen Hand seit über acht Jahren dafür ein, dass neue Technologien und Materialien für ein ressourcenschonendes Bauen soweit entwickelt werden, dass sie den Sprung in den Markt schaffen.
>> Nie mehr eine wichtige Neuigkeit aus der Baubranche verpassen? Abonnieren Sie unseren viel gelesenen Newsletter! Hier geht’s zur Anmeldung!
Jüngstes Beispiel dafür ist die Unit «STEP2». Das zweistöckige Gebäudemodul ganz oben in der Südostecke von NEST vereint eine Reihe von Innovationen, die allesamt zum Ziel haben, den Material- und Energieverbrauch zu senken und einen kreislaufgerechten Umgang mit unseren Ressourcen zu fördern. «Gleichzeitig ist es uns ein grosses Anliegen, dass wir Lösungen entwickeln, die marktfähig sind und in der Baubranche tatsächlich eine Zukunft haben», sagt Enrico Marchesi, Innovation Manager im NEST.
Multifunktionale und ressourcenoptimierte Geschossdecke
Beim Betreten von «STEP2» sticht zuallererst die Decke ins Auge. Als Rippen-Filigrandecke konzipiert, erlaubt sie Spannweiten von bis zu 14 Metern und eignet sich damit besonders für den Büro- und Hochhäuserbau. Entwickelt wurde die Decke vom Architekturbüro ROK zusammen mit dem Ingenieurbüro WaltGalmarini und Stahlton. Mithilfe von eigens entwickelten digitalen Planungsmethoden und 3D-gedruckten Schalungen für die vorgefertigten Elemente konnten sowohl der Materialaufwand wie auch die CO2-Emissionen verglichen mit einer Beton-Flachdecke derselben Spannweite um rund 40% gesenkt werden.
Neben ihrer strukturellen Funktion übernimmt die Decke zusätzlich weitere Aufgaben: Integrierte, 3D-gedruckte Boxen, die mit einem Tonschaum von BASF zur Schallisolation gefüllt sind, sorgen für eine angenehme Raumakustik, trotz schallharter Oberfläche. Ausserdem dient die Decke als thermische Speichermasse, wirkt damit ausgleichend auf die Raumtemperatur und ist ein wichtiger Bestandteil des Energiekonzepts der Unit.
Digital gefertigte Betontreppe
Ins zweite Stockwerk der Unit gelangt man über eine geschwungene Betontreppe mit dem klingenden Namen «Cadenza», die das symbolische Rückgrat des Gebäudes darstellt. Für die Treppe hat das Team rund um den Lehrstuhl «Digital Building Technologies» der ETH Zürich und das Architekturbüro ROK das volle Potenzial von computergestütztem Design und 3D-Druck ausgeschöpft. Die 17 Treppenstufen wurden mit einer einzigen wiederverwendbaren 3D-gedruckten Schalung gefertigt, die eine komplexe und äusserst materialreduzierte Form erlaubt.
Die Vorspanntechnik des Empa-Spin-offs re-fer, die auf einer Formgedächtnislegierung basiert, fixierte die aufeinander gefädelten Stufen. In die Realisierung des auffälligen Bauteils floss zudem die Expertise der ehemaligen BASF-Tochtergesellschaft Forward AM und New Digital Craft im Bereich Material und 3D-Druck der Schalung, sowie des Betonfertigteile-Herstellers SW Umwelttechnik und des Ingenieurbüros WaltGalmarini ein.
Gemeinsam haben sie eine einsatzreife Lösung für individuelle Bauvorhaben entwickelt, die sich nicht nur für massgeschneiderte Betontreppen eignet, sondern generell aufgrund der digitalen Planung und Fertigung zu effizienten und leistungsstarken Designlösungen beiträgt.
«STEP2» – eine reale Innovationsumgebung
«STEP2» ist als Co-Creation-Plattform und Innovationswerkstatt gedacht. Die Unit wird dem «Scouting & Academic Collaborations»-Team von BASF rund um Olivier Enger fortan als Arbeitsplatz dienen. Bereits seit mehreren Jahren pflegen BASF und die Empa eine strategische Partnerschaft; das Team ist seither auf dem Empa-Campus angesiedelt. Olivier Enger ist überzeugt: «Im NEST sind wir an der Schwelle zwischen Forschung und Wirtschaft und können mit unserer Expertise viel für einen erfolgreichen Brückenschlag zwischen Labor und Markt beitragen.»