Großes Interview I Schalung : „Hohe Effizienzsteigerungen“
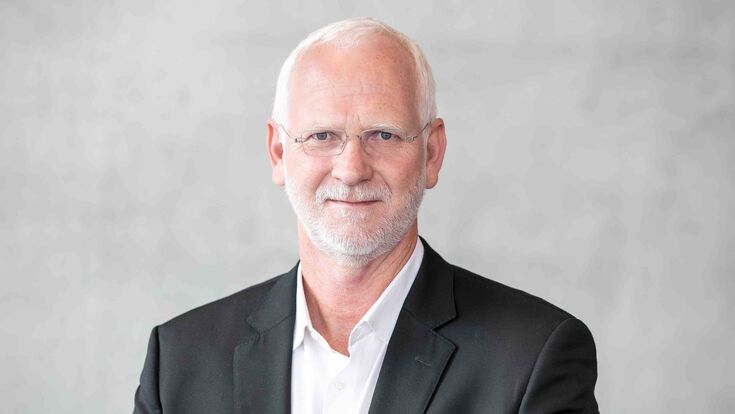
Peter Radel ist gelernter Techniker und die Faszination für Technik und in der Praxis machbare wirtschaftliche Lösungen ist im Gespräch deutlich zu spüren.
- © achim reissnerLean Management
Solid: Vor Ihrer Rückkehr nach Österreich haben Sie einige Jahre und vor allem zur Zeit der schlimmsten Krise in Griechenland gearbeitet. Weilr wir hier so gerne von Krisen reden: War es dort wirklich so übel oder wirkte das nur für unsere mitteleuropäischen Augen so?
Peter Radel: Das war wirklich tragisch. Es haben sich Ärzte zusammengeschlossen, um Menschen zu behandeln, die einfach keine Versicherung und kein Geld mehr gehabt haben. Die Familien helfen unten schon mehr zusammen als bei uns. Wenn einer arbeitslos wird, dann stehen die anderen da und fangen ihn auf.
Aber wenn alle ihren Job verlieren, kann man zuschauen, wie die Geschäfte zusperren. Und wir mussten auch zuschauen, wie unsere Kundenfirmen zusperren, weil der Staat ihnen Geld geschuldet hat und sie ihre Steuerschulden nicht zahlen konnten.
Sie sind dann also nach Österreich übersiedelt und haben hier zunächst gemeinsam mit Christian Sorko das Team geführt. Dieser hat dann eine andere Aufgabe inenrhalb von peri übernommen und später die Firma verlassen. Was betrachten Sie als Ihre wichtigsten Erfolge und Aufgaben bei Peri Österreich?
Eine wichtige Sache hat schon gemeinsam mit Christian Sorko begonnen, nämlich dass er damals als Peri-Österreich-Geschäftsführer die Erlaubnis bekommen hat, in Organisation und Material zu investieren. Wenn ich denke, wie wir gearbeitet haben, als ich gekommen bin, und wie jetzt die Prozesse laufen - das ist schon ganz etwas anderes.
Können Sie da etwas ins Detail gehen?
Ein großes Thema von mir war, dass wir uns die Prozesse im Lager genau angeschaut haben. Der ganze Rücklieferreinigungsprozess, da haben wir doch einiges in Lean Management investiert und das kommt uns auf jeden Fall jetzt zugute. Wir haben ja teilweise 40 Leiharbeiter gehabt und kommen jetzt komplett ohne Leiharbeiter aus.
Investition von 2 Millionen Euro
Können Sie das auch beziffern?
Wir haben ca. zwei Millionen investiert. Begonnen haben wir 2020 mit der Digitalisierung des Rücklieferprozesses mithilfe von Mobile Logistics. Geplant ist auch noch die Digitalisierung des Auslieferungsprozesses. Dazu kommen eine Business Steering App für die Verfolgung von Prozesskennzahlen und Shopfloormeetings.
Allgemein können wir hohe Effizienzsteigerungen verzeichnen. Die Materialflüsse wurden und werden komplett reorganisiert. Es gibt zum Beispiel eine neue Waschstraße für Wandschalelemente – diese Neugestaltung hat eine Reduktion der Fahrwege für Stapler und Kranzeiten für Materialtransporte bewirkt und in Summe den Durchlaufzeit des Return Prozesses von über 21 Tage auf 7,6 Tage reduziert.
Das betrifft alles das Mietsegment, korrekt?
Ja. Generell wird ja kaum mehr etwas wirklich gekauft. Gekauft wird eine Schaltafel, gekauft werden die Einbauteile. Und wenn ich irgendeine Sonderlösung habe, dann habe ich eine Sonderlasche, die muss gekauft werden. Aber alles andere ist Miete und die besteht wiederum aus neuem und gebrauchten Material.
CNC-Maschine um 400.000 Euro
Wie berechnen Sie das?
Wir behandeln alles Material, das der Kunde in Miete hat, als gebrauchtes Material. Wenn jetzt eine Spindel verloren wurde, ist das ja auch nicht abbildbar, oder? - Ist jetzt eine neue Spindel verloren gegangen oder eine gebrauchte? Wenn man das so macht wie wir, ist es eine Win-Win-Situation. Denn von unserer Seite aus wäre das ja auch ein Aufwand, dem nachzugehen. Also das passt für den Kunden und das ist für uns auch in Ordnung.
Und am Schluss, wenn der Kunde dann alles zurückgeliefert hat, dann ist es ohnehin gebraucht.
Was haben Sie noch investiert?
Aus meiner Sicht ist da vor allem unsere neue CNC-Maschine zu erwähnen. Dafür haben wir 400.000 Euro in die Hand genommen, um die gestiegene Nachfrage im Infrastrukturbereich bedienen zu können. Es geht dabei um die Produktion verschiedener Holz-Zuschnitte mit automatischer Be- und Entladung und mit hoher Präzision vor allem für Sonderlösungen. Die Inbetriebnahme ist für das 4. Quartal 2024 vorgesehen.
Vereinfachung durch KI und Digitalisierung
Zuletzt ist auch Ihre Kooperation mit der Firma DataB bekannt geworden – allerdings einmal nur sehr vage. Können Sie dazu mehr sagen?
Mit DataB wird es ein Joint Venture geben (Details sollten im Lauf des Sommers bekannt gegeben werden, Anm. d. Red.). DataB selber ist ein relativ junges Technologieunternehmen und wird auch als solches bestehen bleiben – und die neue gemeinsame Firma wird eine Kooperation auf Augenhöhe sein. Data B als Firma macht weiter die Entwicklung und hat die Software und dort sind jetzt mal die Freaks bleiben. Und diese neue Firma hat zur Aufgabe, dass man sich entsprechend die Erfolge holen kann.
Und das schaut wie aus?
Das ganze Thema ist, dass mithilfe von KI und Digitalisierung die Produktion und Anwendung von Sonderschalungen auf der Baustelle deutlich vereinfach und präzisiert wird. Wir nennen das eine File to Factory Datenintegration.
Um es an einem Beispiel zu veranschaulichen: An einer sehr schön gekrümmten Radwegsunterführung für die ÖBB in Vorarlberg ist ein Techniker bei uns sechs Monate gesessen und andere Techniker haben noch mitgearbeitet - und mit Data B haben wir das in zwei Tagen geplant! Die Konstruktionen, die sie dann machen, sind schraubenlos, also Nut und Feder, das heißt, ich kann das entsprechend zusammenfügen und zusammenstecken und ich kann vor allem sehr schnell einen verlässlichen Preis abgeben – und das wird im Geschäftsleben immer wichtiger.
Neue Beschichtungsanlage
Am Peri-Stammsitz im deutschen Weißenhorn wurden 60 Millionen in eine neue Beschichtungsanlage mit 80 Prozent weniger Energieverbrauch investiert.
„Mit dieser Groß-Investition modernisieren wir unser Schalungswerk Weißenhorn und sind mit dieser Anlage Vorreiter in unserer Branche“, sagte Peri CEO Christian Schwörer zur Eröffnung Anfang Juni 2024. „Unsere Kunden erhalten ab sofort Schalungselemente mit einer innovativen und bis dato in unserer Branche einzigartigen Beschichtung namens PERIskin. Sie bietet einen deutlich besseren Schutz vor Korrosion und setzt gleichzeitig neue Maßstäbe im Hinblick auf Nachhaltigkeit und Energieeffizienz.“
Die Peri-Skin ist ein mehrstufiges Beschichtungsverfahren, das Schalungsrahmen oder auch andere metallische Bauteile wie eine zweite Haut naht- und lückenlos umgibt und auch komplexe Bauteile vor Korrosion schützt. Herzstück des Verfahrens ist VIANT, ein Verfahren, das von Chemetall, der globalen Geschäftseinheit für Oberflächentechnik des Unternehmensbereichs Coatings der BASF entwickelt und gemeinsam mit Peri für die Realisierung der Beschichtung in der neuen Anlage weiterentwickelt wurde.
Das Besondere an dieser innovativen Tauchbeschichtung: Sie findet – im Gegensatz zu bisher üblichen Beschichtungen wie z.B. der Verzinkung - bei Raumtemperatur (20 Grad Celsius) statt und benötigt für den Schichtaufbau keinen Strom.
Deshalb kann mit dieser neuartigen Technologie im Vergleich zu bis dato üblichen Beschichtungsverfahren erheblich Energie eingespart werden. Für eine Beschichtung von Bauteilen mit der Peri-Skin sind nur etwa 5 Prozent der für eine Verzinkung nötigen Energie aufzuwenden. Die für das Auftragen der Beschichtung benötigte Energie bezieht Peri zu 100 % aus dem firmeneigenen Biomasse-Heizkraftwerk.