Großprojekte : Österreich glänzt in der Ferne - drei beispielhafte Top-Projekte
Aktive Mitgliedschaft erforderlich
Das WEKA PRIME Digital-Jahresabo gewährt Ihnen exklusive Vorteile. Jetzt WEKA PRIME Mitglied werden!
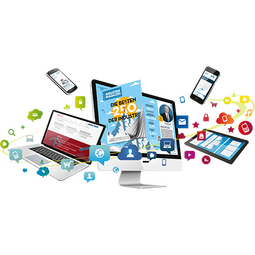
Sie haben bereits eine PRIME Mitgliedschaft?
Bitte melden Sie sich hier an.
Zeig mir deine Baustellen, und ich sage dir, wer du bist – wandelt man einen alten Spruch um und bezieht ihn auf einige aktuelle Projekte heimischer Baufirmen, ist die Antwort ziemlich klar: An der Spitze Europas. Oder der Welt – und es gibt einige, ganz wenige Baustellen, bei denen ist dieses Superlativ nicht einmal übertrieben. SOLID stellt hier drei aktuelle Auslandsprojekte unter Federführung von Österreichern vor. Alle drei demonstrieren besonders gut, wie Bauen fernab der Heimat erfolgreich sein kann. Konkret geht es um die Errichtung einer Großhalle aus Stahl in einem mehr als rauen Markt. Dann eine spektakuläre Dachkonstruktion in London. Und den Bau der weltgrößten Hubbrücke im Hafen von Rotterdam. Tunnels, Autobahnen, EZB, Mt. Saint-Michel und ein Mittelständler Wo Österreicher im Ausland stehen, zeigt zunächst ein kurzer Streifzug durch das Geschehen der letzten Monate. Die Porr baut gerade in Stuttgart, für das derzeit größte Bauprojekt Europas, die zwei technisch am schwierigsten zu errichtenden Tunnel (wir berichteten in SOLID 12/2014). Vor kurzem gewann der Konzern einen weiteren Großauftrag im Tunnelbau: Diesmal geht es um den Bau eines knapp sechs Kilometer langen Tunnels im Schweizerischen Graubünden.Bei der Strabag-Tochter Zueblin laufen unterdessen nach frisch gewonnenem Auftrag die Vorbereitungen für Berlin auf Hochtouren – die Firma baut einen Teil der Stadtautobahn A100. Mitte März hat Frankfurt die - wenn auch politisch umstrittene - Eröffnung seines neuen Wahrzeichens gefeiert, jene des neuen EZB-Hochhauses. Das Gebäude ist als hyperbolisches Paraloid angelegt, bis zu 201 Meter hoch und besteht aus zwei dynamisch geschwungenen Türmen. Das Konzept stammt von Coop Himmelb(l)au in Wien.Und in der Normandie ist seit heuer die geschwungene Stelzenbrücke zum weltberühmten Klosterfelsen Mont Saint-Michel in Betrieb – erbaut vom steirischen Architekten Dietmar Feichtinger. Ein kleiner Teil der Brücke ist überflutbar, für wenige Stunden im Jahr bleibt der Berg weiter eine isolierte Insel. Zugleich ersetzt der neue Steg einen alten Damm, um der massiven Verlandung rund um Mont Saint-Michel entgegenzuwirken. Allerdings sorgen nicht nur glanzvolle Großprojekte für Aufsehen, wie der Mittelständler KLH zeigt. Die Kärntner waren mit speziellen Holzpaneelen am Bau eines neuen Pavillons im Inneren des Eiffelturms beteiligt. Heimische Holzbautechnik also – für die Ikone des Stahlbaus schlechthin. Auf nach Russland – der Krise zum Trotz Für jene, die den Schritt in einen fremden Markt wagen, sind Fragen zur Bautechnologie nur ein kleiner Teil der zu lösenden Schwierigkeiten. Das führt ein aktueller Hallenbau von Pem besonders deutlich vor Augen. Eigentlich sind für den Hallenbauspezialisten Projekte fernab der Heimat alles andere als Neuland – die Oberösterreicher haben schon erfolgreich im Irak, Iran, in Saudiarabien oder Kasachstan gebaut. Der Schritt ins Ausland verschafft Unabhängigkeit von den Schwankungen in den Kernmärkten, denn eine aufkommende Flaute spürt ein klassischer Frühzykliker wie Pem besonders schnell. Deshalb erwirtschaftet das Unternehmen, das zur Zeman Gruppe gehört, heute nur etwa 30 Prozent des Umsatzes in Österreich. Etwa 60 Prozent setzen die Mauthausener in Deutschland um, wo sie sich besonders bei bayerischen Autozulieferern eines hervorragenden Rufs erfreuen. Doch die restlichen zehn Prozent sind geprägt von Mut zum Abenteuer – und Risiko. Seit vielen Jahren ist Pem in Rumänien und der Ukraine präsent. Mitte 2014 entschied Geschäftsführer Thomas Ennsberger, den Sprung nach Russland zu wagen – und das mitten im schweren Konflikt Moskaus mit Kiew und dem Westen. "Wir haben vom Hersteller Knauf einen Folgeauftrag bekommen: den Bau eines Werks für Aquapaneele in Novomoskovsk, rund 150 Kilometer südlich von Moskau. Und da haben wir gesagt: Das ist der Moment, jetzt gehen wir nach Russland", erzählt Ennsberger. Natürlich sei Knauf als Auftraggeber eine gute Absicherung gewesen. Auch bei der Gründung habe es keine Probleme gegeben, so Ennsberger weiter: "Die Zahl der Firmen, die eine Niederlassung in Russland gründen wollten, war sehr überschaubar." Doch im Herbst 2014 ging die Arbeit erst los – und zwar nicht nur auf der Baustelle. Stolz und Selbstbewußtsein – und fehlende Baukrane Die vor wenigen Wochen fertiggestellte Industriehalle misst 9000 Quadratmeter und hat eine freie Spannweite von 54 Metern – an sich beachtliche Maße, aber für den Hallenbauer Routine. Weniger alltäglich wurde die Kooperation mit russischen Stellen, etwa die Materialbeschaffung. "Wir haben nicht Profilstahl gebraucht, sondern Wellstegprofile, eine Spezialität unserer Konzernmutter. Also waren wir in Russland angewiesen auf eine einzige Firma, die später wegen der aktuellen Entwicklungen massive Liquiditätsprobeme bekommen hat", so Ennsberger. Nicht der einzige Grund für schlaflose Nächte und kurzfristige Flüge nach Osten. An Stolz und Selbstbewußtsein mangele es den Russen nicht, erzählt der Pem-Chef. Doch in der Zusammenarbeit mit lokalen Baufirmen seien selbst alltägliche Aufgaben wie die Beschaffung von Kränen und Hilfsmitteln eine Herausforderung – mit entsprechenden Auswirkungen auf die Geschwindigkeit beim Bau. Schließlich ist auch die unterschiedliche Mentalität ein Faktor. "Was am Tisch gesprochen und was tatsächlich gemacht wird, sind zwei verschiedene Sachen." Doch davon lassen sich die Oberösterreicher nicht beeindrucken – sie arbeiten weiter daran, den riesigen russischen Markt zu erschließen. Auch ein anderes fernes Land wartet bereits: Pem ist kurz davor, einen Großauftrag in Angola zu bekommen. Ennsbergers Rat: "Man darf nicht seine Abläufe 1:1 in einen fremden Markt übertragen. Ohne umfassende Anpassung wird das nicht klappen." London: BBC berichtet von der Baustelle Von Russland zu einer Metropole Westeuropas – nach London. Im Geschäftsviertel Canary Wharf entsteht gerade nach einem Entwurf von Norman Foster die Canary Wharf Crossrail Station. Das Dach haben die oberösterreichischen Baufirmen se-austria und Wiehag 2014 fertig gestellt. Beide können auf zahlreiche besondere und bereits mehrere gemeinsame Projekte im Ausland verweisen. Wiehag spezialisiert sich auf anspruchsvolle Holzbauten, se-austria gilt als Spezialist für komplexe Dach- und Fassadenkonstruktionen aus Glas, Membranen, Stahl, Aluminium oder Holz. Doch das Londoner Projekt ist nicht nur das aufsehenerregendste im Portfolio beider Firmen – die BBC berichtete gleich mehrfach über die Bauarbeiten, mittags pilgern Geschäftsleute an den Bauzaun. Die Bauingenieure beider Firmen geben heute auch zu, die spezifische Technologie der Konstruktion sei sowohl für se-austria als auch für Wiehag Neuland gewesen. Die Eckdaten: Für das 300 Meter lange und 30 Meter über Wasser auskragende Dach des Bahnhofs lieferte Wiehag das tonnenförmige Holz-Schalentragwerk, auf das se-austria mit der Kissenkonstruktion aufsetzte. Dafür montierten die Bauleute vor Ort 780 Membrankissen auf 1.414 Brettschichtholz-Elemente. Technisch besonders anspruchsvoll sei die Kombination von Holzunterkonstruktion und ETFE-Kissen, heißt es bei se-austria. Die pneumatischen Luftkissen, die aus Ethylen-Tetraflourethylen bestehen, sind gegen Witterung besonders beständig und sorgen für eine filigrane Optik, wie man sie etwa vom Münchener Allianz-Stadion kennt (siehe auch SOLID 03/2015, Material World). Änderungen "auf Knopfdruck" Stark vereinfacht, war der Ablauf so: Innerhalb von nur sechs Monaten produzierte Wiehag am Standort Altheim die notwendigen Brettschichthölzer aus heimischem Nadelholz und montierte sie zum Dachtragwerk an der Themse. Noch bevor die Landsleute fertig waren, begann se-austria mit dem Einsetzen der ETFE-Kissen. Sie stammen aus der Produktion der Augsburger Konzernmutter Seele. In London übernahm se-austria die Entwicklung, Konstruktion, Fertigung und Montage der Aluminiumklemmprofile, der maßgeschneiderten Abdeckbleche als Witterungsschutz der im Freien liegenden Holzträger und der Regenrinnen. 330 Luftverteilerkästen für den permanenten Luftaustausch zwischen den zweilagigen Kissen. Die Übergabe an den Bauherrn erfolgte pünktlich – nicht zuletzt wegen des Einsatzes einer speziellen Berechnungsmethode, des „Parametric Design". Dabei haben die Ingenieure möglichst viele Planungsbereiche in das parametrische Konstruieren mit einbezogen, berichtet se-austria. Daten zu Prozessen und Fertigungsdaten wurden miteinander verknüpft. Wenn sich nun ein bestimmter Parameter geändert hatte, geschah die Anpassung aller anderen davon betroffenen Elemente automatisch. Das Ergebnis dieser Methode: Anpassungen der Pläne und Datensätze waren „auf Knopfdruck“ möglich, technische Änderungen unabhängig vom Zeichenaufwand. Im Sommer 2015 geht die Station in Betrieb. Norman Foster findet die Umsetzung offenbar schon heute super: Im Foyer des weltbekannten Architekturbüros hängt seit kurzem ein übergroßes Wandbild vom neuen Dach der Canary Wharf Crossrail Station. Rotterdam: Ein Hub von 10.000 Tonnen pro Stunde Auch die Botlek-Brücke geht im Sommer 2015 in Betrieb – die größte Hubbrücke, die jemals gebaut wurde. Die Neuerrichtung der Botlek ist der schwierigsten Teil bei der Erweiterung der A15 quer durch den Rotterdamer Hafen. Wie von SOLID bereits berichtet, sind Österreicher auch an diesem Bau federführend beteiligt: Für den gesamten Milliardenauftrag ist das Baukonsortium A-Lanes unter der Führung der Strabag verantwortlich. Bei der Botlekbrücke übernimmt A-Lanes den Tiefbau und alle Teile aus Beton. Die Generalplanung für den Brückenbau sowie für den Stahl- und Betonbau liegt beim Ingenieurbüro Vienna Consulting Engineers. Und Waagner-Biro aus Wien plant, liefert und montiert die gesamte M&E-Technologie – jenen Teil also, der dafür sorgt, dass das hochkomplexe Bauwerk tatsächlich „lebt“. Die Leistung der Waagner-Biro bei der Mechanik umfasst den gesamten Antrieb, alle Seile und Seilrollen, Verriegelungen und Führungssysteme für die zwei Stahldecks und die Gegengewichte. Bei der Elektrik die gesamte Energieversorgung und das Steuerungssystem. Wenn die Brücke fertig ist, tragen ihre beiden Stahldecks fünf Autobahnspuren, einen Radweg – und zwei Eisenbahngleise. Jedes Stahldeck misst stattliche 92 Meter Länge. Beide können unabhängig voneinander so weit hoch fahren, dass unten bequem ein Hochseefrachter durchpasst – und das, obwohl jeder Hub mit einem einzelnen Brückenteil plus seinen zwei Gegengewichten 10.000 Tonnen in Bewegung setzt. Etwas anderes ist noch außergewöhnlicher: die extrem hohe Geschwindigkeit beim Öffnen und Schließen, die extrem hohe Anzahl von 9000 Öffnungen pro Jahr, also etwa jede Stunde, und die extremen Anforderungen an die Zuverlässigkeit der Technologie – schließlich handelt es sich hier um eine zentrale Zufahrt zu einem der drei größten Häfen der Welt. Hier eine knappe Skizze der Konstruktion: Die Brückenpfeiler, in die diverse Führungsschienen eingelassen sind, ruhen auf einer Flachgründung. Die Pylone sind etwa 60 Meter hoch. Oben auf jedem Pylon sitzen acht wuchtige Umlenkrollen aus Stahl, jede einzelne mit einem Durchmesser von 3,6 Metern und einem Gewicht von zwölf Tonnen. Wenn alles fertig ist, funktioniert der Antrieb – stark vereinfacht – so: In den Betonpfeilern sitzen starke Elektromotoren. Diese sind über Getriebe mit Seiltrommeln verbunden. An diesen Seiltrommeln sind die sogenannten Hubseile befestigt. Diese sind einerseits mit dem Stahldeck und andererseits mit dem Gegengewicht verbunden. Zusätzlich sind das Stahldeck und das Gegengewicht mit den sogenannten Gegengewichtsseilen verbunden. Der Showdown im Herbst Letzten Herbst kam es schließlich zum Showdown, den der staatliche Auftraggeber Rijkswaterstaat und A-Lanes extra in Internetvideos der Öffentlichkeit vorstellen. An einem bestimmten Tag wurde das erste der beiden, jeweils 5000 Tonnen schweren Stahldecks am kilometerweit entfernten Vorzusammenbauplatz auf rund 500 (!) SPMT-Schwerlastachser gehoben, auf einen schwimmenden Ponton geladen und zur Brücke geschleppt. Dann fuhr das neue Stahldeck längs durch die alte Botlekbrücke durch und wurde am nächsten Morgen zeitgleich mit der Ebbe in Position gebracht, bis alle vier Enden des Kolosses exakt an den vorgesehenen Stellen "angeschlagen" haben. Danach begann der noch schwierigere Teil der Arbeit: Das Stahldeck an die extrem komplexe Mechanik und Hydraulik und die zwei Gegengewichte anzuschließen. Und zwar maximal innerhalb von 40 Stunden, die die Hafenbehörde den Baufirmen für die Sperrung der Wasserstraße zugestanden hat. Das Kunststück ist trotz des enormen Zeitdrucks gelungen. Bei aller Bescheidenheit – nach mehrmaligem Nachfragen geben die Beteiligten bei diesem Bau schließlich eines zu: Es gibt weltweit nur sehr wenige Firmen, die ein Projekt wie die Botlekbrücke umsetzen könnten.
Erschienen in SOLID 04/2015